SAM Updates
SAM Updates
April 8, 2009: Update from Amy McAdam, SAM Science Team Member: SAM Science Team Meeting Summary
On Monday, March 2nd, members of the SAM science team met at Goddard Space Flight Center to discuss the SAM instrument's testing and calibration status and SAM-related science topics. A SAM overview and status talk was presented by SAM PI Paul Mahaffy, followed by updates from the Tunable Laser Spectrometer (TLS) lead Chris Webster and Gas Chromatograph (GC) lead Michel Cabane. SAM-relevant laboratory derivitization and isotope studies being carried out in the Atmospheric Experiments Lab at GSFC were also discussed. Science updates from the recent Mars mission Phoenix were presented by members of the Phoenix science team. There is some overlap between the types of analyses carried out by instruments on Phoenix and those that will be conducted by SAM. Therefore Phoenix results, such as the detection of the mineral calcite and perchlorate salts, are especially relevant for consideration during SAM calibration and interpretation of future SAM data from the surface of Mars. In addition, logistical aspects of future SAM mission operations were discussed, such as operations training, organization of surface science experiments, and mission data access.
March 25, 2009: Update from Lora Bleacher, SAM Education and Public Outreach Lead: SAM to be Topic of Presentation at the 40th Lunar and Planetary Science Conference
Tomorrow, SAM PI Paul Mahaffy will present an overview of the SAM instrument suite at the 40th Lunar and Planetary Science Conference at The Woodlands, TX. The presentation will be featured during the "Science Instruments for the Mars Science Lander" session at 1:30pm. Click here to see the schedule of talks and to download the abstract about SAM.
March 24, 2009: Update from Lora Bleacher, SAM Education and Public Outreach Lead: Vote to Name the Mars Science Laboratory Rover!
From now through March 29 you can vote to name the Mars Science Laboratory rover on which SAM will investigate Mars! http://marsrovername.jpl.nasa.gov/
December 23, 2008: Update from Lora Bleacher, SAM Education and Public Outreach Lead: SAM Employee Day Featured in December Issue of "Goddard View"
The December 2008 issue of "Goddard View" features an article on SAM's successful Employee Day on page 3.
December 8, 2008: Update from Lora Bleacher, SAM Education and Public Outreach Lead: SAM Holds Successful Employee Day
On Friday, December 5, SAM team members hosted 85 Goddard employees for Employee Day. Seven tours of the SAM facilities were led by team members throughout the day. The tour stops included a viewing of various movie clips and interviews with team members, a peek inside the cleanroom where SAM is currently undergoing environmental testing in the Mars simulation chamber, a discussion with SAM team members who are monitoring SAM while it's being tested, and an opportunity to see a scale model of the SAM suite and to view an animation of the landing and operation of the Mars Science Lab rover.
December 4, 2008: Update from Lora Bleacher, SAM Education and Public Outreach Lead: MSL Launch Rescheduled for 2011
On Thursday, December 4, NASA Headquarters announced that it will be delaying the launch of the Mars Science Laboratory rover until the fall of 2011. The launch had to be rescheduled in order to allow for additional testing of hardware on the rover that is essential for its success. Click here to learn more.
December 2, 2008: Update from Paul Mahaffy, SAM PI: SAM Operating in Mars Environment Chamber
SAM is now operating in the Mars environmental chamber such that all major elements are operating at Mars' ambient pressure (7 torr). The suite is receiving twenty-four hour coverage by the Thermal, Software, and Chamber Operations Teams. Although the SAM teams were fully prepared and willing to work through Thanksgiving Day, Goddard Management insisted they take a well-deserved break to eat turkey and celebrate. Both the GC and TLS teams will remain at Goddard through at least the end of this week to test their instrument s within the chamber.
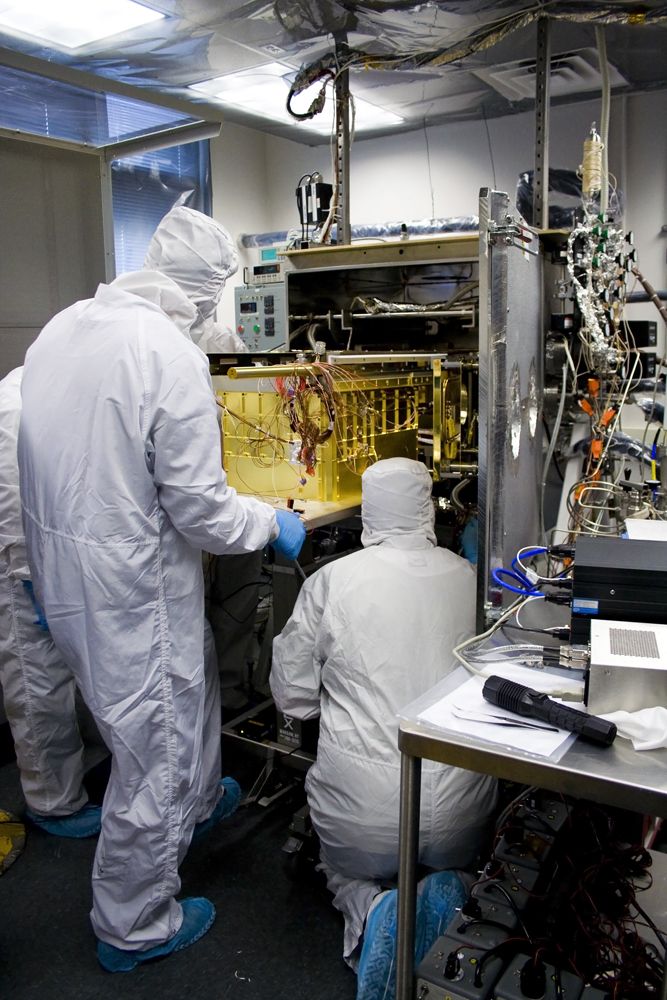
SAM going into Mars environment chamber.
November 26, 2008: Update from Daniel Glavin, SAM Planetary Protection Lead: Calibration Material Loaded into Sample Manipulation System (SMS) Cups for Testing Inside Ma rs Chamber
Last Thursday, several small metal cups containing a solid calibration material were inserted into SAM. The metal cups designed by John Bishop were lowered into the quartz cups in the sample manipulation system (SMS) through the solid sample inlet tube (SSIT) by a medical device used in surgery. The solid sample calibration material consists of calcium carbonate, iron sulfate, and fused silica that will be used to "ground-truth" the SAM flight instrument inside the Mars chamber.
Surgical medical device used to insert solid calibration material.
Insertion of calibration material into SMS via SSIT.
November 20, 2008: Update from Gregory Flesch and Didier Keymeulen, TLS Team: TLS Undergoes Diagnostic Testing
Two members of the Tunable Laser Spectrometer (TLS) team from JPL, Gregory Flesch (Software Lead) and Didier Keymeulen (Electronics Lead), are visiting Goddard this week to boot up the TLS and run diagnostic testing. They will be performing dry-runs of the scripts that will be performed once SAM goes into the thermal vacuum Mars simulation chamber later this week. The testing will use the TLS reference cells which contain well-known quantities of both methane and carbon dioxide to assure that the instrument's laser and detector are working properly.
November 3, 2008: Update from Carol Lilly, SAM Integration and Testing Lead: SAM SAM Progress Briefing on Halloween
Every month, the SAM project manager, Doug McLennan, presents the teams' progress not only to the Goddard Space Flight Center management, but also to managers from Jet Propulsion Lab. These meetings are not necessarily held at the same time, but this October's meeting was an exception with both briefings occurring on Halloween. The SAM team was happy to report that instrument integration was complete minus the Main Electronics Box which would be installed that day. After some final harnessing, preliminary testing and minor remaining closeouts, we would be ready for thermal vacuum testing to begin in early November. Below are some photos showing both the current configuration of SAM and also the SAM team.
SSIT installation.
SAM Main Electronics Box undergoing safe-to-mate.
SAM Champion Team meeting.
Directors meeting.
SAM Team meeting.

SAM PI, Paul Mahaffy, on Halloween.

Dave on Halloween.

Mike on Halloween.

Paula on Halloween.

Kyle on Halloween.

John on Halloween.
October 27, 2008: Update from Florence Tan, SAM Electrical Systems Engineer: SAM Main Electronic Box (MEB) to be Installed this Week
The SAM team's goal is to install the Main Electronics Box (MEB) and its 1100 wires (about � kilometer total length) into the SAM suite by the end of this weekend. Bob Arvey has been working diligently to complete the harnessing in the SAM suite over the last several months. As the harnessing was completed and the subsystems installed, the rest of the Electrical and Software Team performed "safe-to-mates", which are tests to confirm that the harness pins worked correctly. In addition, power checks have been performed on each of the subsystems. Two tests, the Aliveness and Electrical Baseline Tests, were run this week. The MEB will be installed after the data from these two tests is analyzed. After the MEB is installed, the team will run another Electrical Baseline Test to confirm that all of the wires are delivering the right electrons to the right subsystem.
SAM electronics during Electrical Baseline Test.
SAM electronics undergoing electrode test.
October 27, 2008: Update from Oren Sheinman, SAM Mechanical Lead: Solid Sample Inlet Tube Successfully Integrated
Last week, the Solid Sample Inlet Tube (SSIT) assembly was successfully integrated onto the Sample Analysis at Mars (SAM) suite. The SSIT represents the doorway to the SAM suite through which a solid sample is received from the Mars Science Laboratory (MSL) rover robotic arm for processing to the three on-board instruments within SAM. The sample can be di rected down either one of two funnels on top of the SSIT and down through a delivery tube into a cup where it is positioned for pyrolysis and analysis. The funnels vibrate during sample receipt by an internal piezo actuator which helps to provide full sample delivery and to minimize the potential for sample clogs in the delivery tubes.
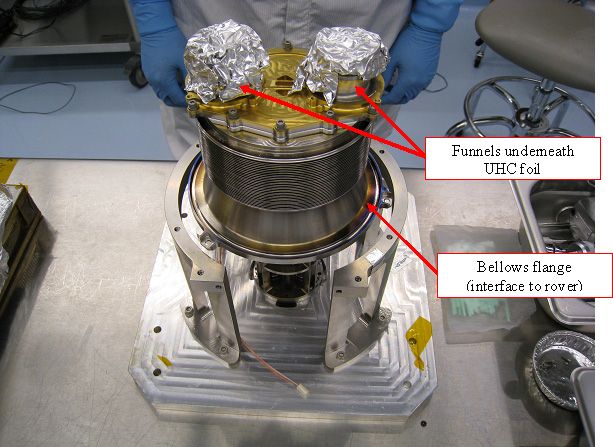
SSIT pre-installation.
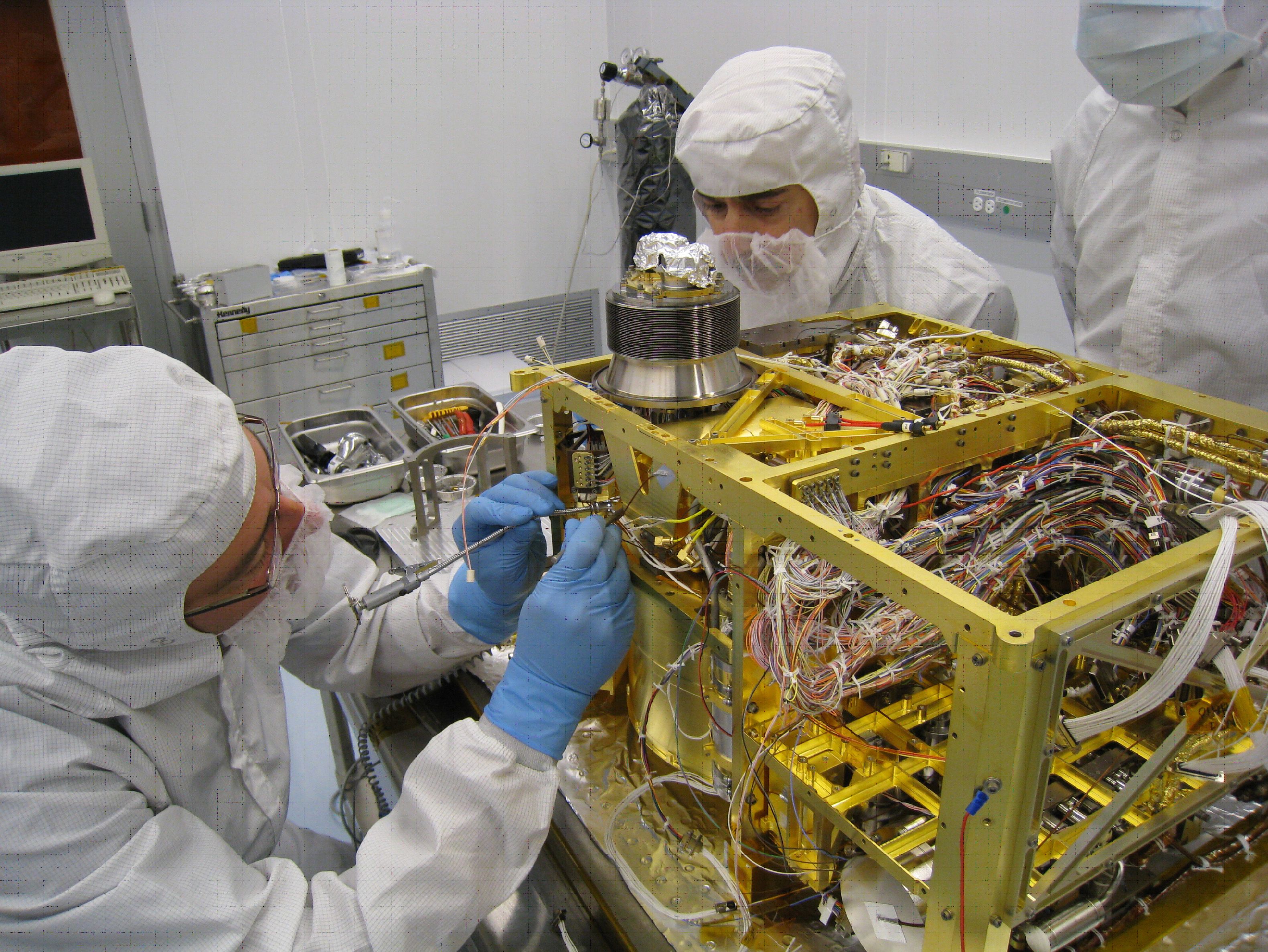
SSIT during integration.
SSIT integration was performed in two stages. The first fastened the base of the unit to the mid-plate �shelf� which precisely registers or positions several key components to each other for successful sample delivery. A vacuum tight seal was required to keep out contamination for future testing under ambient conditions throughout the test program before launch. The second stage fastened the upper section or bellows flange to the top frame to provide a closeout to the rover. Once the integration was completed, the position of the funnels and the closeout plane of the bellows flange were determined using a precision Faro Arm measurement device. This provided placement or positional knowledge good to 0.002 inches to verify SAM is compliant to interface placement requirements to the rover.
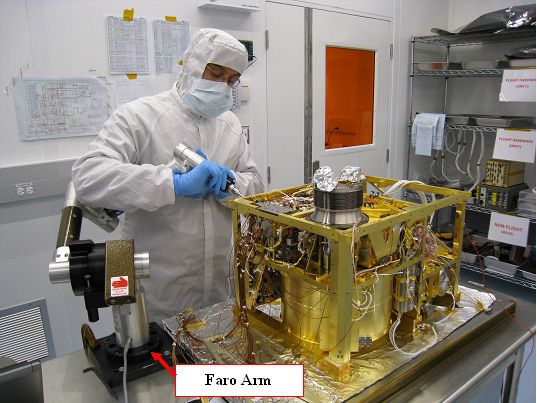
SSIT funnel position being checked with Faro Arm.
The integration process was completed by installing ground support equipment (GSE) vacuum caps with o-rings onto the funnels and the seals were leak-checked successfully to demon strate that they could hold vacuum conditions.
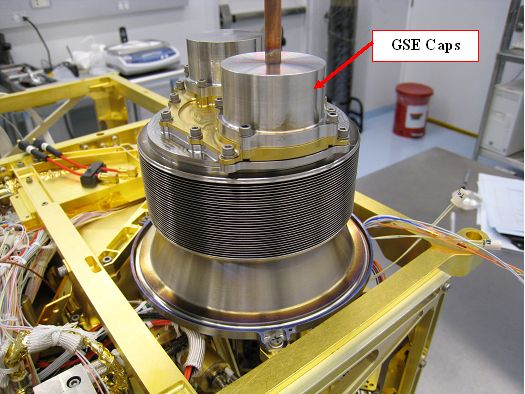
SSIT with GSE caps.
October 15, 2008: Update from Jason Feldman, SAM Instrument Engineer: Development of SAM Mechanical Pathfinder Procedures in Progress
SAM engineers are in the process of developing the procedures, tools, and equipment that will be needed for integrating SAM into the Mars Science Laboratory rover. Although the actual integration probably will not take place until February 2009, it is imperative to test the procedures and tools now. A mechanical pathfinder of SAM has been created for this purpose. Essentially a shell of the SAM instrument suite without instruments, the mechanical pathfinder will be delivered to JPL later this month to be integrated into the Mars Sc ience Laboratory development test model (DTM). The DTM is similar to SAM's mechanical pathfinder in that it is a shell of the MSL rover. Testing the procedures for integration of the mechanical pathfinder will take approximately 3 days. The procedures for integrating SAM's electronics with those of the rover will also be tested using an engineering model o f the electronics. This testing will probably take about one week.
October 10, 2008: Update from Nick Kwiatkowski: SAM's Four Heat Pipes Successfully Bonded
SAM's heat pipes were successfully bonded to the instrument suite last week. There are four heat pipes on SAM, each of which is designed to carry heat away from specific compone nts. The heat pipes are bonded with Nusil, a silicone Thermal Conductive Bonding Agent that gives a better conductive joint than just metal to metal contact. The condenser of each heat pipe rejects heat into the SAM top frame, which is hard mounted to the rover interface plate.
The silicone bonding operation took place in the clean room where SAM is currently being prepared. Special precautions where set in place for this operation to prevent the spread o f cross contamination, which included suiting up in disposable Tyvek suites and being confined to a secluded Mylar tent.
The areas where the heat pipes are located are in tight, hard to reach, obstructed areas. It was imperative to make sure no silicone touched or got onto any of the other components because of cross contamination. The job was very tedious and required working against the clock due to the short pot life of the bonding agent, but the Integration team was up for the challenge and prevailed victoriously.
SAM with bonded heat pipes.
October 3, 2008: Update from Paul Mahaffy, SAM PI: Sample Manipulation System Cups Installed and Tested
SAM's Sample Manipulation System (SMS) developed by Honeybee Robotics(Eric Mumm, lead engineer) and driven by a Goddard-developed electronic circuit (Dave Sheppard, lead engineer) was populated with the sample cups, tested, and covered to keep this critical sample path clean. A primary SAM experiment serviced by the SMS is pyrolysis. Samples delivered from the MSL sampling system on the rover's arm are passed into SAM's vibrating Solid Sample Inlet Tube (SSIT) to a quartz cup contained in the SMS. The SMS then delivers the sample cup to a sealed position in an oven where it is heated to drive off volatile species, such as water, and oxides of carbon and sulfur (if minerals containing these elements are present). If the sample contains organic molecules these compounds or their pyrolysis products may also be released for further analysis by the SAM instruments.
View the SMS during testing in this video (to download Quicktime, click here).
September 26, 2008: Update from Paul Mahaffy, SAM PI: SAM Science Team Participated in Science Team Meeting and MSL Landing Site Workshop Last Week
A summary of SAM development and a good discussion on a variety of topics occurred at the SAM mini science team meeting last week in Pasadena. The topics presented included: 1) SAM status, 2) education and public outreach activities and plans, 3) analog studies, 4) landing sites, and 5) MSL/SAM operations plan status. Attending were Sushil Atreya, Michel Cabane, Patrice Coll, Pan Conrad, Paul Mahaffy, Steve Squyres, Chris Webster, Danny Glavin, Jen Eigenbrode, Cyril Szopa, Mehdi Benna, Amy McAdam and the MSL Project Scientist John Grotzinger who led a landing site criteria discussion. Doug Ming and Dick Morris who had planned to attend got caught by hurricane Ike and hunkered down in Texas.After the workshop, most SAM science team members stayed in CA for the third Mars Science Laboratory Landing Site Selection Workshop in Monrovia. Relevant material and meeting presentations can be found at http://marsoweb.nas.nasa.gov/landingsites/. The current top 3 landing site options are: Nili Fossae Trough, Holden Crater, and Mawrth Vallis.
September 10, 2008: Update from Lora Bleacher, SAM Education and Public Outreach Team: Learn about SAM at Goddard's LaunchFest on September 13, 2008
This Saturday, Sept. 13, from 10am to 4:30pm, Goddard Space Flight Center in Greenbelt, MD will open its doors to the public for the first time in 4 years. The purpose of LaunchFest is to celebrate all of the recent and upcoming launches for which Goddard has built the spacecraft or instrument hardware. SAM and MSL will be one of the highlighted instruments / missions. View a scale model of SAM, learn how the Mars atmosphere simulation chamber is used to test SAM under the conditions it will experience on the surface of Mars, and view videos and animations about SAM and the exciting MSL mission. To learn more about LaunchFest, visit http://www.nasa.gov/centers/goddard/events/launchfest.html. We hope to see you there!
September 4, 2008: Update from John Canham, Senior Staff Scientist/ATK Space providing contamination control support for the SAM instrument: SAM Bake-out Complete
Gas Chromatography-Mass Spectrometry (GC-MS) was used to analyze contaminants caught in traps during several flushes of the SAM gas path with argon during bake-out. These analyses allowed us to assess how much and what types of contaminants were present and how their concentration or type changed as bake-out progressed. This was important in determining that the system was getting cleaner with time. Additionally, the analyses allow the evaluation of the contaminants' impacts on the SAM instrument data space. These analyses will also help us to distinguish between system contaminants and martian compounds in SAM results from the surface of Mars.
August 27, 2008: Update from Roc Chalmers, SAM Thermal Subsystems Lead: SAM Bake-out Underway!
The SAM suite-level bake-out is at last underway! During bake-out, the SAM instrument suite is taken to high temperature for the purpose of driving out molecular contaminants. During instrument integration, some unwanted molecules tend to collect on the interior surfaces of the instruments, gas transfer lines, valve manifolds, and other nooks and crannies along the gas flow path. By driving the hardware to a high temperature, these condensed contaminants are vaporized and swept out of the instrument via the lab vacuum system. This procedure is somewhat analogous to cycling a self-cleaning oven to remove accumulated crud.
As of Tuesday evening, the bake-out had progressed to 100°C. Following a flush of the SAM gas path with ultra-pure carbon dioxide, the bake-out will continue under vacuum at even higher temperature. By Thursday, we expect to be at our goal temperature of 200�C. SAM will remain at this high-temperature plateau until the residual gas analyzers (RGAs) tell us that the instrument suite is thoroughly clean.
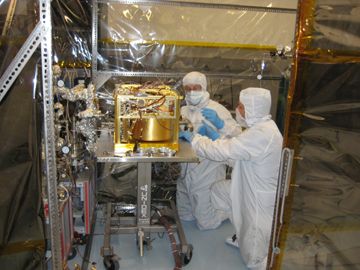
Over the weekend, SAM engineers were hard at work preparing SAM for bake-out.
August 14, 2008: Update from Carol Mosier, SAM Thermal Design Engineer: Preparations Underway for SAM Suite Bake-out
It has been a particularly busy time for the SAM thermal team. We are currently preparing for the suite bake-out, which will remove all traces of moisture and contamination from the suite before it undergoes thermal vacuum / thermal balance (TV/TB) testing. During bake-out heaters will raise the temperature of the Gas Processing System, QMS instrument, and plumbing lines to 200°C. SAM's thermal/electrical/system/mechanical personnel have worked together to design, build, and integrate this complex set-up for the bake-out.
Planning and hardware integration for the TV/TB test is well underway. There is a lot of test hardware that is associated with the thermal test. Chris Johnson is leading the effort to get our new Mars environment chamber ready (see the Update from August 6, 2008). Mario Martins is coordinating the development and testing of our cooling plate and chiller system. This will simulate MSL�s Freon fluid loop for our TV/TB test. Benny Pratts is supervising the installation of test heaters and sensors on the SAM suite.
TV/TB testing will consist of three parts. The first part of the testing, which will bake-out the electronics, will take place in a vacuum to simulate the cruise phase of the mission while MSL is on its way to Mars. The second part of the testing will take place under Mars-like atmosphere conditions in the Mars simulation chamber. SAM will be cycled over its full temperature range and performance tests/mini-calibrations will be done. TB testing will be performed during this part also. For TB individual components will be heated to assess both steady-state and transient performance in order to correlate thermal models of how SAM should function. Last, the Mars simulation chamber will go back to vacuum conditions, in order to do a final contamination certification of SAM.
August 8, 2008: Notes from the Lab from Kristen Mihalka, SAM Research Scientist: In Her Own Words...
I am a PhD student from the University of Michigan working on SAM. This summer I was privileged enough to come to Goddard to work on SAM. This experience has taught me a great deal. I come from a scientific background and I am very used to being given data or creating a model to get data. This was my first experience with the engineering side of things. It is truly amazing the amount of work everyone puts in to complete the instrument on time. Before this summer, I did not have the proper appreciation for the engineers who make it possible for scientists to collect data.
Here at Goddard I have worked mostly with the calibration of different aspects of SAM. For part of my time here, I worked with the QMS and for the other part I worked with the pyrolysis ovens. With the QMS, I worked with a gas calibration that was conducted during the month of May. Here we are trying to better understand how the instrument works as well as figuring out what a natural background is for the instrument. This is important for when SAM arrives at Mars because it helps us determine what is Martian, as well as, how precisely we can measure different compounds. I will continue to work on this calibration after my tenure at Goddard has ended and will then compare it to the next gas calibration done after the bake out.
With the pyrolysis ovens, a comparison was done between the sense wire and the thermal couple to decipher the true temperature. When the sense wire was taken out attempts were made to see if the resistance could be used to derive temperature and how accurately this can be done. Recently, we have been performing lifecycles. Each pyrolysis oven has to complete about 80 runs on Earth. I have been working to determine how closely the cycles correlate to each other and making sure that there are no anomalies. Finally, a run has been done with a sample in the oven. I have been working to understand how this changes the temperature profile and how we can predict the results of future sample runs. We have also attempted to replicate the dip in the profile that occurred due the samples presence using a temperature derived from the resistance.
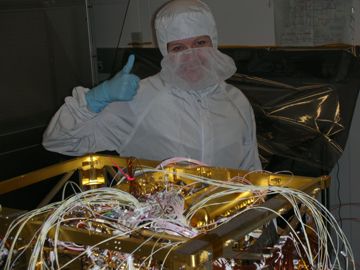
The above photo is of Kristen in the SAM cleanroom.
August 7, 2008: Notes from the Field by Jason Feldman, SAM Instrument Scientist: 1st Blog Entry from the AMASE 2008 Expedition
Jason Feldman is blogging from Svalbard during the Arctic Mars Analogue Svalbard Expedition (AMASE). The purpose of the expedition, an annual event since 2003, is test teh equipment and procedures needed to look for the evidence of organic chemistry and possibly life on Mars. Jason will be blogging on a regular basis from Svalbard. Check out the blog on the AMASE Website.
August 6, 2008: Update from Christopher Johnson, SAM Programmer: SAM Soon to Undergo Testing in Mars Simulation Chamber
SAM will soon undergo thermal vacuum / Mars environment testing at the Goddard Space Flight Center Mars Calibration Laboratory. The Mars environment / space simulation chamber is capable of reproducing the predicted extremes of pressure, Mars atmosphere and thermal conditions to be encountered by SAM during the Mars Science Laboratory rover mission.
The SAM thermal boundaries are maintained by 5 actively controlled shroud plates and 1 chiller plate. A shroud plate mimics the rover's compartment walls that surround SAM. The chamber is thermally controlled by a liquid nitrogen separator vessel which serves as a cold gas source to 5 independently controlled cryogenic valves. The shroud plates are heated by resistive cartridge elements. The SAM suite is directly mounted to the chiller plate which is controlled by an independent recirculating chiller unit. SAM will be exposed to a minimum temperature of -50C and maximum of +70C during testing. The tests should take approximately 3 weeks to complete.
The Mars chamber is nearing completion of the Pre-Environmental Review - Certification contamination bake out in preparation for receiving the SAM suite. The bake out will remove all traces of moisture and contamination from the chamber before the testing of SAM begins.
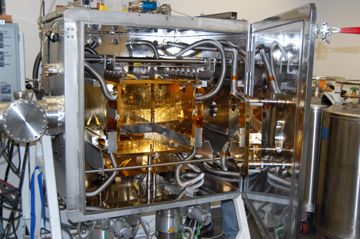
The above photo is of the Mars Chamber in which SAM will soon undergo Mars environment testing.
July 21, 2008: Update from David Martin, SAM System Engineering Lead: SAM Undergoes Pre-Environment Review (PER) This Week
SAM will undergo its Pre-Environmental Review (PER) this week. The PER is one of a series of "gated process" reviews that SAM must undergo before it is cleared for shipment to JPL to be integrated onto the Mars Science Laboratory rover. The PER precedes a series of environmental tests that are dedicated to demonstrating that the flight hardware will perform correctly during launch, landing, and operations on the surface of Mars. Many of the individual parts of SAM have already undergone such testing. Now it is time for SAM as an integrated suite to undergo the tests. At the PER, the SAM team will present to a panel of independent experts the pressure, temperature, vibration, shock, and electro-magnetic radiation levels and margins that the environmental tests will encompass. SAM is expected to operate at pressures of 6-12 torr and temperatures between -40 C and +50 C while on the surface of Mars; however its survival levels must cover a larger range of values.
During the course of the environmental tests, a Comprehensive Performance Test (CPT) is run five times. The CPT trends the characteristics of the most important SAM suite performance parameters, while the hardware is experiencing the extremes of the conditions which it will see on Mars. The data from this set of tests is analysed for SAM�s ability to measure the required signal/noise and verify that performance is not degrading with time or by the environments. After completing the PER and the associated environmental testing, SAM will have to complete a Pre-Ship Review before being sent to JPL.
July 18, 2008: Update from Micah Johnson, Flight Scripts: SAM Gas Chromatograph Team Completed Valve Addressing Test
The SAM Gas Chromatograph (GC) team completed a Valve Addressing Test (VAT) last week. The purpose of the VAT was to make sure that the flight model's valves work as they should (i.e., the valves are not clogged, wires are connected properly, etc.). Each of the GC's 6 columns was pumped down in a vacuum to make sure that the valves were empty of air before the test. Ultra pure research-grade Helium was then pumped through the valves. Pressure monitors at the ends of the valves monitored the resulting rise in pressure. The VAT took approximately 6 hours to complete because it took approximately 20 minutes to pump down each column and then 40 minutes to add Helium and monitor the rising pressure within the valves. According to the results obtained with the pressure monitors during the VAT, SAM's GC valves are working properly.
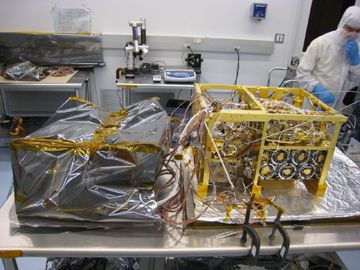
The above photo is a picture of the test configuration. The covered item to the left is the MEB (i.e. SAM's computer). The structure to the right is SAM. You can see the GC (six circles) on the lower right of SAM. One of the tubes coming into the system from the upper right provides helium. The other is attached to a pump. The fellow on the far right is Benny Prats, a Thermal Systems Engineer on the SAM project.
July 11, 2008: Update from Benny Prats and Rudy Foxwell, SAM Thermal Systems: Last Pipe Tested Before Being Fitted on SAM
This week, Pipe 34, the last of the 58 pipes in SAM, was wrapped and underwent heater testing so that it can be integrated onto the SAM Flight Model. This particular pipe will open to let the Mars atmosphere into SAM's Tunable Laser Spectrometer (TLS) through Manifold 15. The atmospheric gas will be heated to 135°C to prevent condensation before it enters the TLS. The TLS will measure the isotopic ratios and abundances of these species in the gas: H2O, CH4, CO, CO2, OCS, H2O2, and N2O.
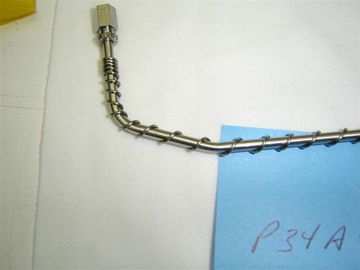
The above photo is a closeup of half of Pipe 34, wrapped in heater coils, and connected to the Manifold 15 / TLS fitting. The heater coils are in contact with the pipe in most areas, however, gold covered aluminum foil will eventually be used to cover the heaters to form an "oven" effect. Notice also that the fitting has a temporary "cover" to make sure particulates do not enter the "gas path" interior to the pipe.
July 1, 2008: Update from Mike Barciniak, SAM Electronics: SAM Hardware and Software Undergo "Dummy" Testing
Last week, a comprehensive flight-like configuration of Heater Loads and Temperature Sensor simulators ("dummy loads") was completed. These simulators were successfully used to run and analyze a baseline test on the SAM Engineering Model and will help verify hardware and software operations of the entire suite on while on Mars. They will be moved to the Flight Model this week for pre- and post-vibration test verification on the SAM Main Electronics Box, and later for SAM integration and testing with the Rover at JPL in October 2008.
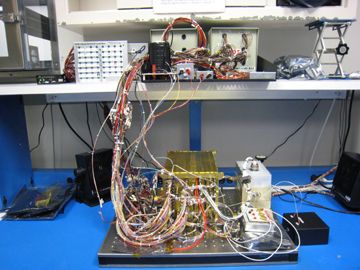
In the above photo, the heat and temperature simulators are the boxes labeled "hot." The SAM flight model is coated in gold foil.
June 19, 2008: Synthia Tonn, SAM Mechanical Engineer, featured in current issue of GoddardView and video
The June 2008 issue of "GoddardView" features an article on Synthia Tonn, SAM Mechanical Engineer, on page 10. To download the free Adobe Reader, click here.
Learn more about Synthia and her work with this video (to download Quicktime, click here).
June 17, 2008: SAM Mechanical Engineer featured in May issue of "GoddardView".
The May 2008 issue of "GoddardView" features an article on Jesse Lewis, SAM Mechanical Engineer, on page 11. To download the free Adobe Reader, click here.
June 12, 2008: Update from Oren Sheinman, SAM Mechanical Lead
Integration of the QMS instrument onto the SAM Instrument Suite was completed last week. As you can see in the picture, assembly of the �Swiss watch� we call SAM is progressing. The SAM instrument suite is scheduled for delivery to JPL in October 2008 and the MSL Rover is scheduled to launch from KSC in September 2009.
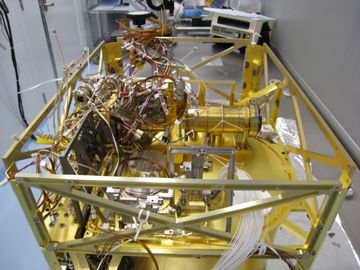
SAM Instrument Suite
June 5, 2008: Follow the Carbon on Mars with SAM
This article from ChemMatters magazine explains why SAM wants to follow the carbon on Mars. Learn more about ChemMatters. To download the free Adobe Reader, click here.
May 14, 2008: Video of Jesse Lewis, SAM mechanical Engineer
Jesse talks about his work with SAM (to download Quicktime, click here).
May 12, 2008: Report from Paul Mahaffy, SAM PI
The SAM quadrupole mass spectrometer (or QMS as its known to the SAM team) that is designed to measure gases on Mars is being baked out this week prior to integration into the SAM frame. The QMS is made of ultra-high-vacuum compatible materials, such as titanium alloys, that can withstand high temperatures. We raise the temperature of the QMS to above 200 degrees Celsius (that's 392 Fahrenheit, or 473 Kelvin) for several days while it is being pumped by an ultra-high-vacuum turbomolecular pump. This high temperature bake removes residual contamination such as hydrocarbons that are prime detection targets on Mars from the instrument. The picture of the QMS shows the vacuum housing and valves that will introduce martian gas to the instrument when we are on Mars. Also shown are heaters wrapped around the QMS that will bring the instrument to the desired bakeout temperatures both in the laboratory and when we are on the surface of Mars just a couple of years from now. Since this is such a critical process, we'll repeat the bake after the QMS is integrated with the rest of the SAM instruments and components and before MSL is put on its rocket and launched to Mars.
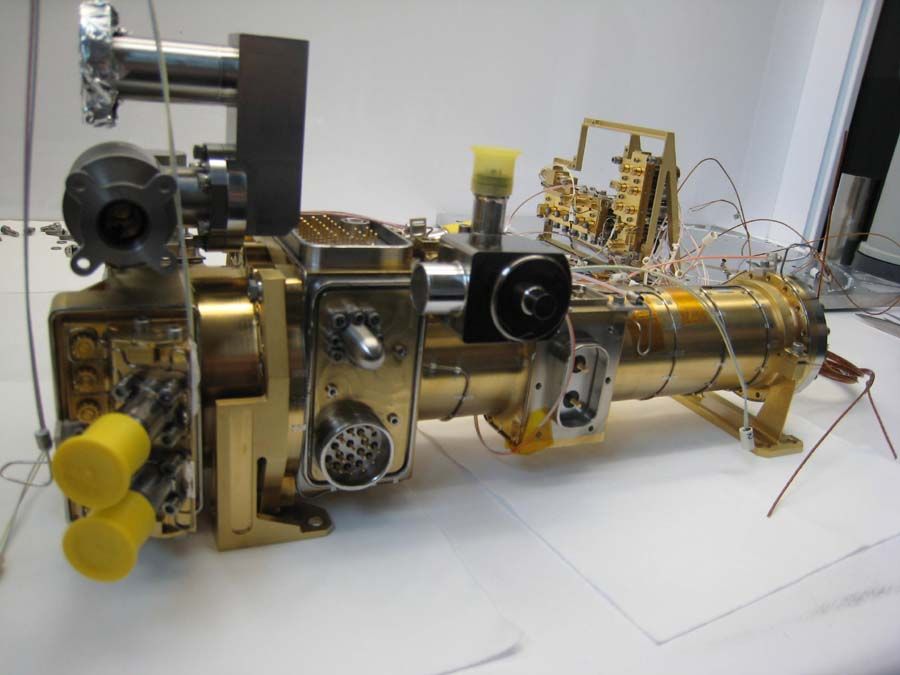
SAM quadrupole mass spectrometer